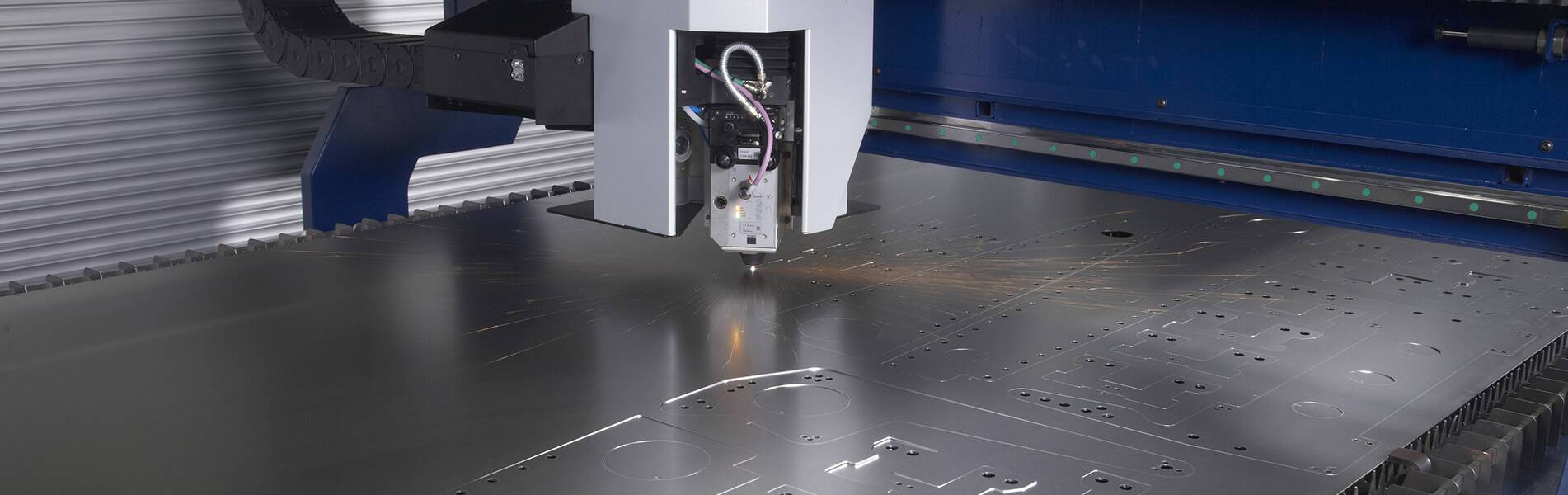
Search
The rapid development of science and technology brings about the improvement of production level. With the rapid development of industry, advanced metal stamping technology has been widely used in our country. Now let's talk about what metal stamping is and its advantages: 1、 What is metal stamping Metal stamping is a processing method of cutting and forming metal plate or coil by using punch and ...
Material selection of stamping parts: The three most important steps in a stamping factory are shearing, punching / cutting and folding. Stamping parts are sometimes used as metal pulling. The word comes from English platemetal. Generally, some metal sheets are pressed by hand or die to produce plastic deformation to form the desired shape and size, and more complex parts can be formed by welding ...
In terms of structure, the convenience of feeding, ordering, discharging and waste cleaning shall be ensured as far as possible. For the processing of small parts, it is strictly prohibited for the operator's fingers, wrists or other parts of the body to extend into the mold area for operation; For the processing of large parts, if the operator has to work in the mold by hand, the scope of enterin...
At present, the commonly used materials of metal stamping parts are: 1) SECC: galvanized iron sheet 2) Spec: tinned cold rolled sheet 3) Sus: stainless steel series 4) Al: aluminum series 5) Cu: copper series 6) PBR: white copper 7) Spte: Tinplate 8) Al set: lamp cover 9) Al Arg: lamp cover
Stamping process and its characteristics stamping is a pressure processing method that uses the die installed on the press to exert pressure on the material at room temperature to produce separation or plastic deformation, so as to obtain the required parts. Stamping is usually cold deformation processing of materials at room temperature, and mainly uses sheet metal to process the required parts, ...
Hardware stamping factory has strict inspection standards, which are divided into sampling inspection and all inspection. Sampling inspection, also known as sampling inspection, is a statistical method and theory to randomly select a small number of products (samples) from a batch of products for inspection, so as to judge whether the batch of products are qualified or not. It is different from co...
Metal processing plants often encounter burrs in metal stamping parts when producing metal stamping products. There are tools to remove the burr of metal stamping parts: 1. Hole: use a chamfering knife or the front end of a larger diameter drill bit 2. Edge: use file, oilstone, sandpaper, grindstone, 3. Welding slag: vibration slag removal tools can also remove brittle burrs 4. Outer diameter: gui...
The three most important steps in a stamping factory are shearing, punching / cutting and folding. Stamping parts are sometimes used as metal pulling. The word comes from English platemetal. Generally, some metal sheets are pressed by hand or die to produce plastic deformation to form the desired shape and size, and more complex parts can be formed by welding or a small amount of mechanical proces...
The processing of metal stamping parts is the requirements for bending parts: 1. The shape of bending parts shall be symmetrical as far as possible, and the bending radius shall not be less than the minimum bending radius allowed by the material. 2. The curved edge is too short and difficult to form, so make the straight part of the curved edge H > 2 δ。 If h is required to be very short, approp...
Why is the surface quality of metal stamping parts poor? There are many reasons for the surface quality problems of stamping parts. For example, the surface quality of coil, sheet and die will affect the quality of stamping parts. The operation in the stamping process and the clamping, taking and unloading of station instruments may also damage the surface quality of stamping parts. Therefore, the...
Usually, sheet metal is the material for the plate type, which is generally made into the specified shape and operated by the plate shearing machine or bending machine, while the machining is more complex. The material is massive, not simply bent and deformed, but cut, etc. the equipment generally uses lathes, grinding machines, etc
During the production and processing of stretch stamping parts, there will be tension cracks. Do you know why tension cracks occur? How to deal with this situation? When the tensile stress on the cylinder wall exceeds the strength limit of the material during the processing of tensile stamping parts, the product will crack, and the crack usually appears at the cylinder wall slightly above the fill...
1
2© Copyright: 2024 Jiaxin (Xiamen) Precise Metal Co.,Ltd. All Rights Reserved
IPv6 network supported